90+
Devices Connected
65+
Smart Hardware Access Points
9,000+
Active Users
Stanley Black & Decker (SBD), headquartered in New Britain, Connecticut, USA, is a global leader in tools and solutions. The company operates in over 175 countries and employs more than 50,000 people. In 2024, SBD ranked 263rd on the Fortune U.S. 500 list with a reported revenue of $15.781 billion.
SBD is the world’s second-largest lithium-ion power tool brand. It owns iconic names like DEWALT, Stanley, and Black+Decker, which hold a strong presence in global markets. By driving technological innovation, committing to sustainability, and leveraging its global reach, SBD continues to lead the industry.
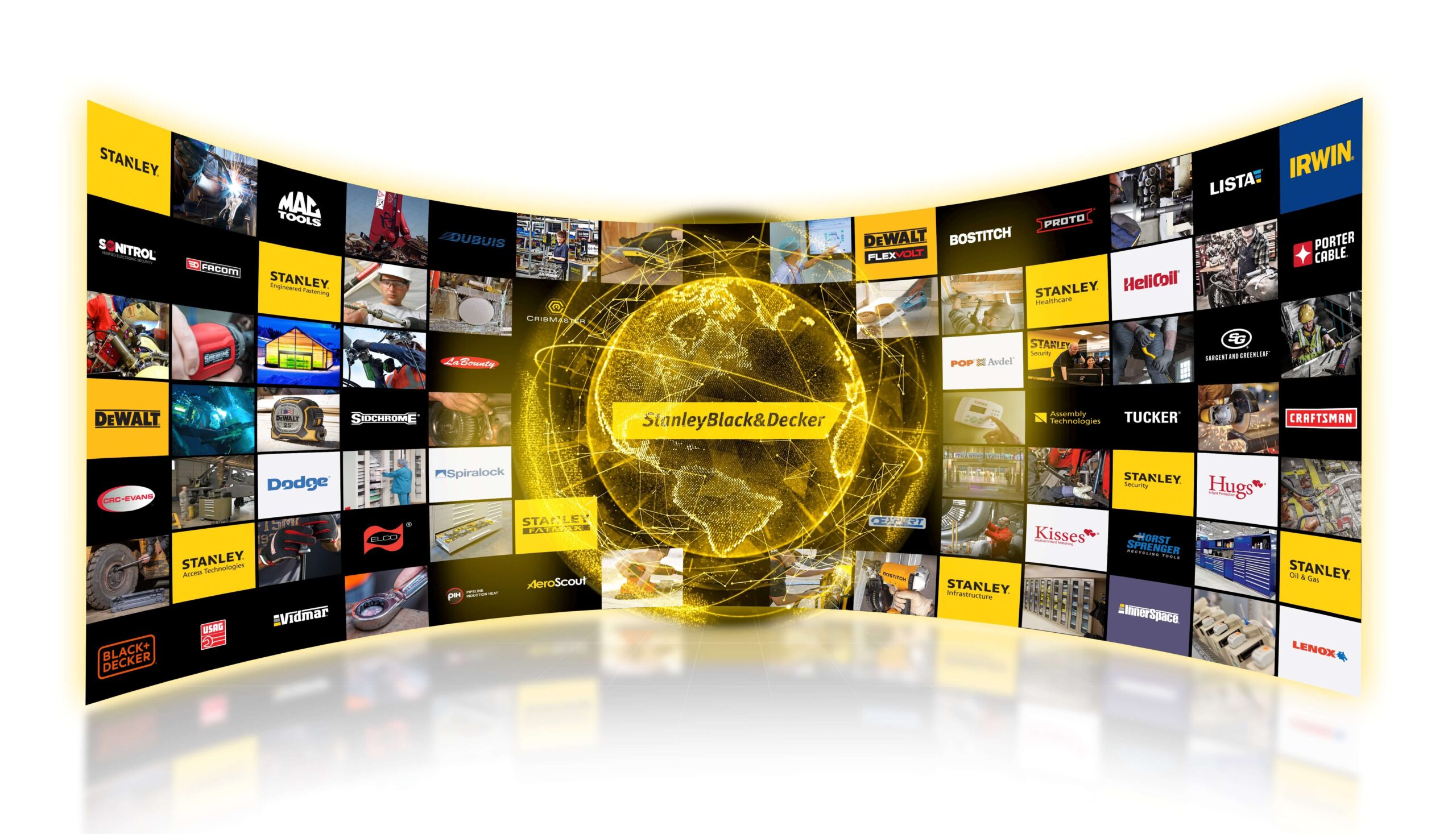
The Challenges
SBD encountered several operational challenges that hindered efficiency and performance:
Complex Equipment Management
Managing asset records, inventory, maintenance schedules, and equipment status became increasingly challenging due to the distribution of workshops and equipment across various factory areas, buildings, and floors. The diversity of automation equipment and inconsistent data protocols added further complexity to integration and tracking.
Inefficient Spare Parts Management
Spare parts were managed through a “three warehouses and five distribution points” model spanning 480 square meters. Over 50,000 transactions annually were handled by six staff members working in two shifts. The outdated PC-based inventory system resulted in long approval processes, inefficient part retrieval workflows, and difficulties in tracking spare part usage accurately.
Vendor Management Challenges
Communication with vendors for non-standard equipment and MRO (Maintenance, Repair, and Operations) products relied on fragmented channels like phone calls, emails, and paper documents. This lack of traceability led to frequent issues with specification mismatches, delivery delays, and time-intensive reconciliation processes.
Lack of Performance Visibility
Equipment asset management spanned 8 departments, 2,175 employees, and 15 vendors. This created inefficiencies in data tracking and process execution. Inconsistent data formats hindered performance monitoring and made KPI tracking nearly impossible.
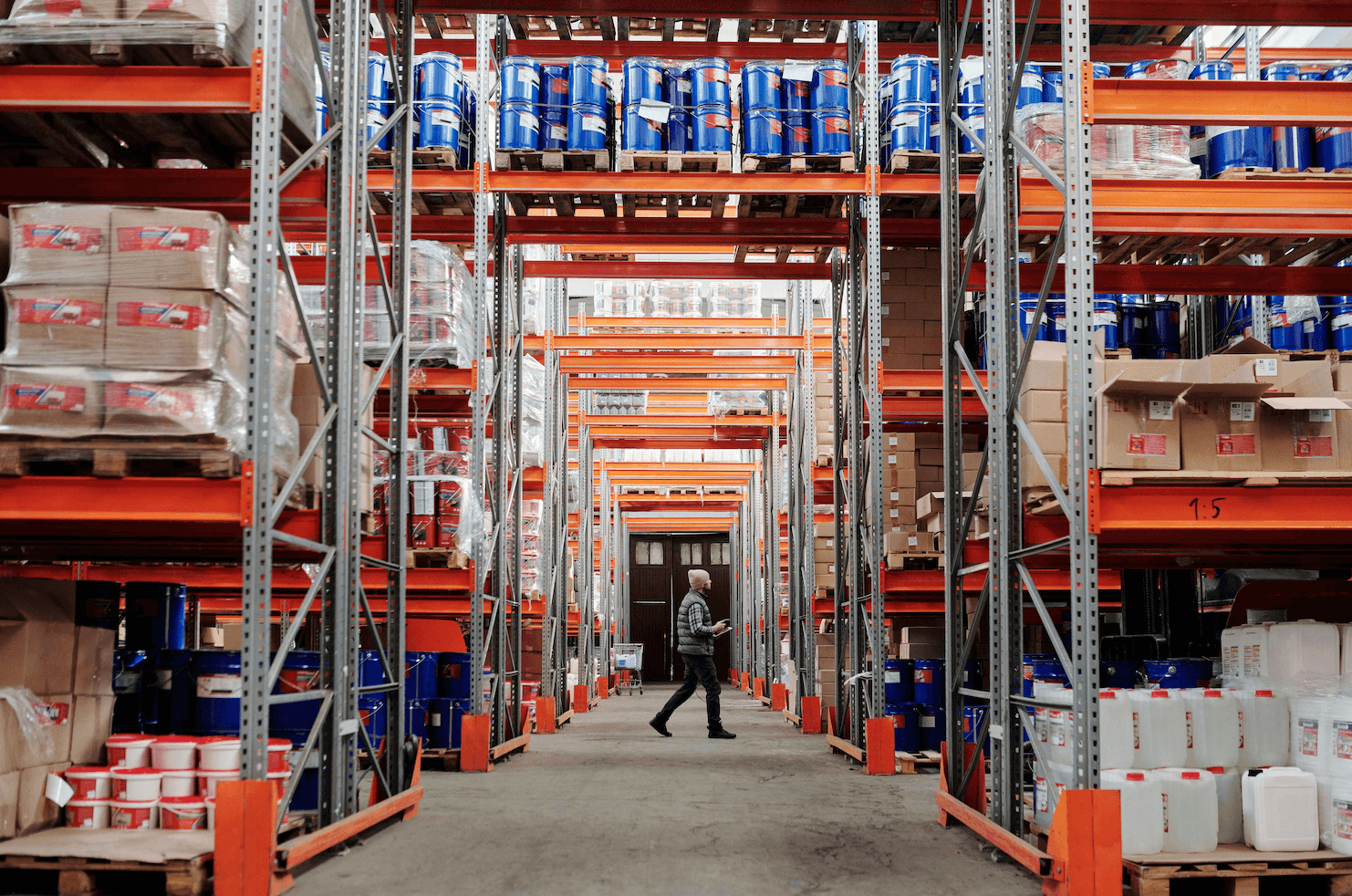
Solution Overview
To address these challenges, SBD partnered with Jodoo to implement a solution and initiate the “Digital Smart Trilogy: Equipment Edition.” This initiative aimed to modernize equipment management processes and achieve a fully connected Digital Smart Factory.
The solution was implemented in three key phases:
Process Optimization
Leveraging Jodoo’s no-code form capabilities to streamline workflows and standardize processes.
Device Interconnectivity
Standardizing device data formats to enable real-time communication between hardware and software systems.
Data Empowerment
APIs are used to connect systems, hardware, and Jodoo for seamless data tracking, real-time flow, and closed-loop management for better decision-making.
Key Features of the Solution
- Automatic fault detection and repair request triggers without manual intervention or code scanning.
- Real-time repair progress updates for enhanced visibility.
- Integration with SRM (Supplier Relationship Management) system and smart warehouse management for automated spare parts retrieval and supplier self-restocking with “use-first, pay-later” functionality.
- Comprehensive operational data tracking for improved performance monitoring.
Implementation Scenarios
Scenario 1: Enhancing Maintenance Efficiency Through Device Interconnectivity
SBD integrated device management data with Jodoo to address inefficiencies in repair workflows. Standardizing device PLC (Programmable Logic Controller) and IPC (Industrial PC) data formats enabled real-time connectivity between devices and Jodoo’s platform.
This integration allowed for real-time data collection on device operation, faults, output, and quality metrics. Automatic alarms were triggered based on predefined thresholds, generating repair requests instantly. The new system also introduced a “grab order” mode for repair work orders, linking historical repair records and escalating unassigned tasks automatically.
Results:
- Fault response time was reduced to near-instantaneous levels with 100% accuracy in repair request generation.
- Production anomalies were addressed 60% faster, improving production rate achievement significantly.
- Data-driven repair work order management enabled complete performance evaluation.
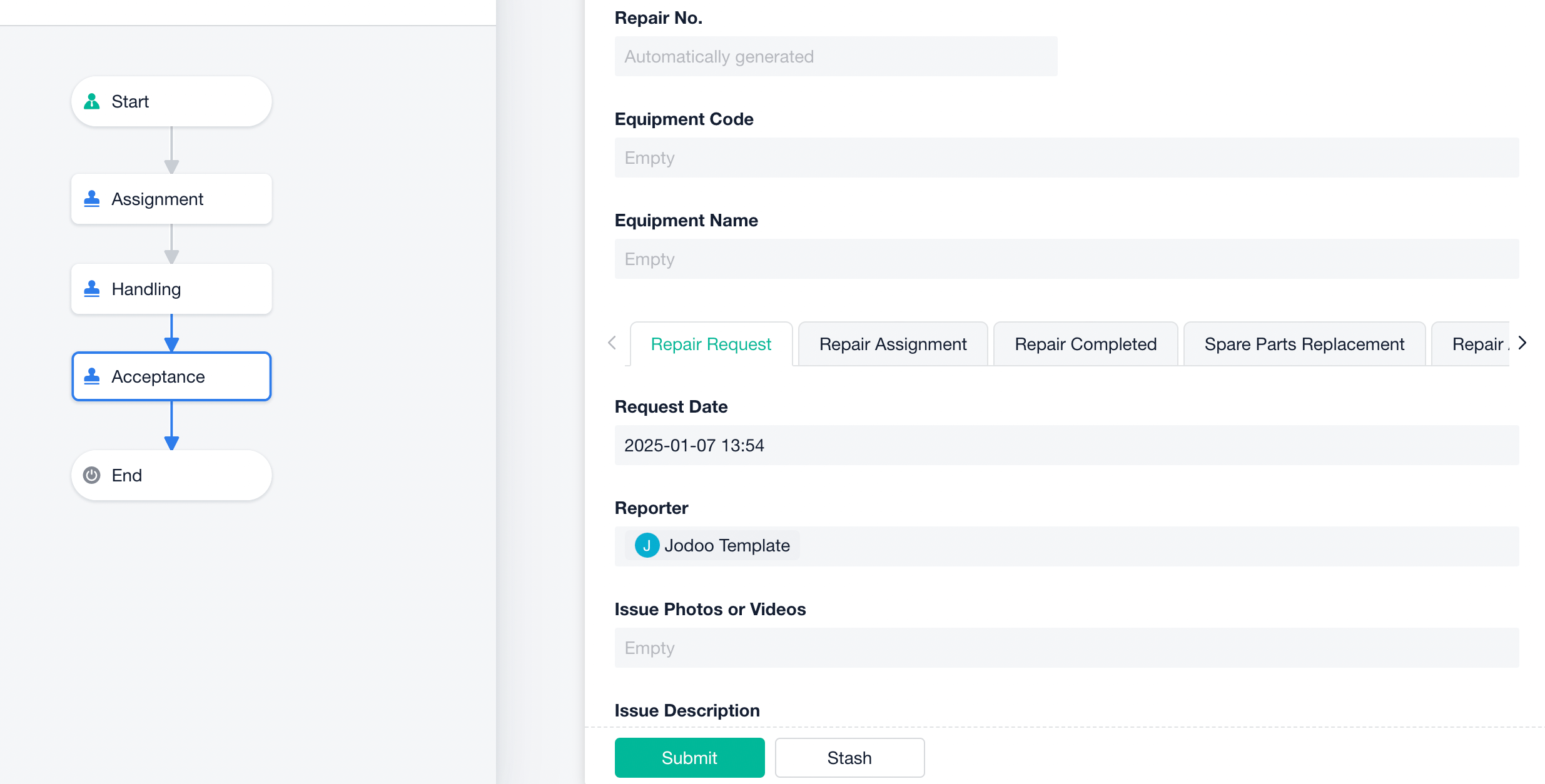
Scenario 2: Streamlining Vendor Collaboration with SRM
SBD revamped its vendor collaboration processes by implementing Jodoo’s SRM application. This platform automated key procurement workflows such as inquiry management, order comparisons, and delivery tracking. The system also generated delivery notes and invoices automatically for seamless entry upon receipt.
Additionally, smart spare parts cabinets equipped with facial recognition and weight sensors were introduced to enable quick retrieval of parts by repair personnel while ensuring accurate inventory tracking.
Results:
- Vendor communication efficiency increased by 80%, with traceability reaching 100%.
- Automated procurement workflows improved accuracy and reduced approval cycles significantly.
- Spare parts retrieval time reduced to under 1 minute per transaction.
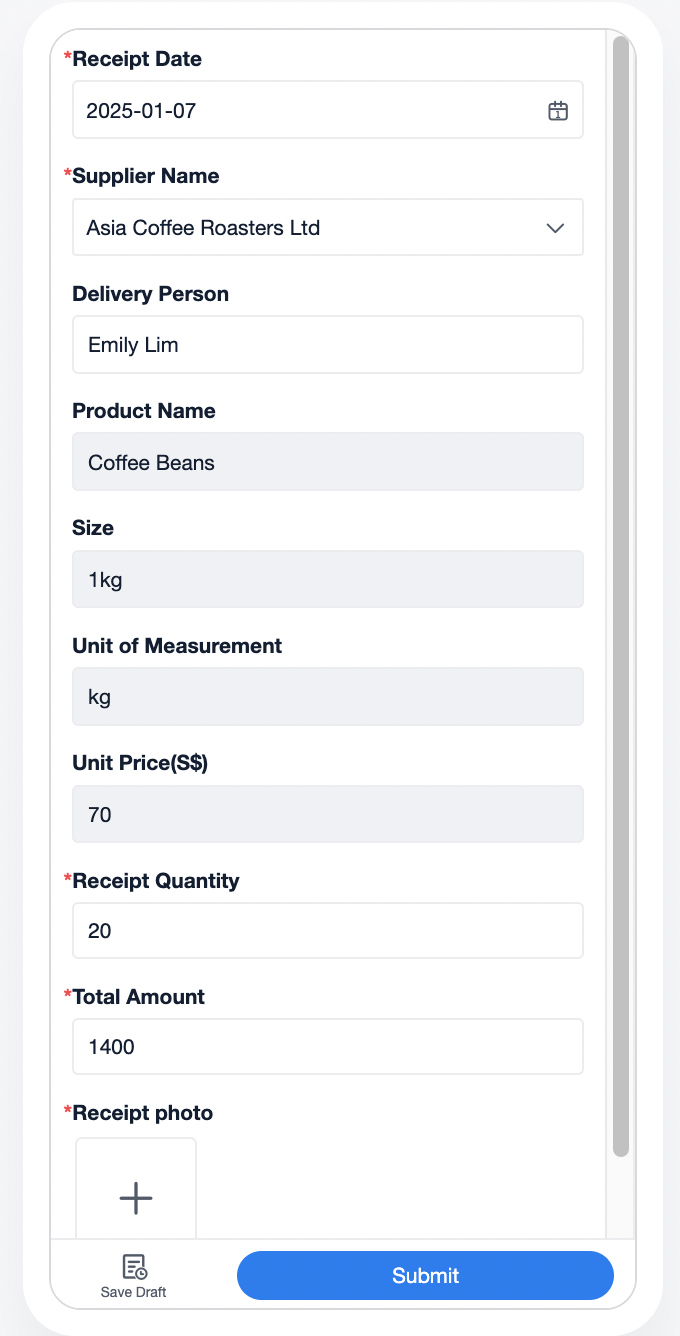
Scenario 3: Driving Fair Performance Management Through Data Tracking
To address inefficiencies in performance evaluation, SBD used Jodoo to collect behavior data across departments and vendors. By leveraging data analysis tools within Jodoo, they implemented a transparent performance assessment mechanism for both employees and suppliers.
This approach allowed SBD to establish fair KPIs for employees while performing periodic evaluations of supplier performance. High-performing suppliers were rewarded with increased collaboration opportunities, fostering stronger partnerships.
Results:
- Enhanced fairness and transparency in employee performance reviews fostered a more competitive work environment.
- Supplier service quality improved through consistent evaluations and feedback loops.
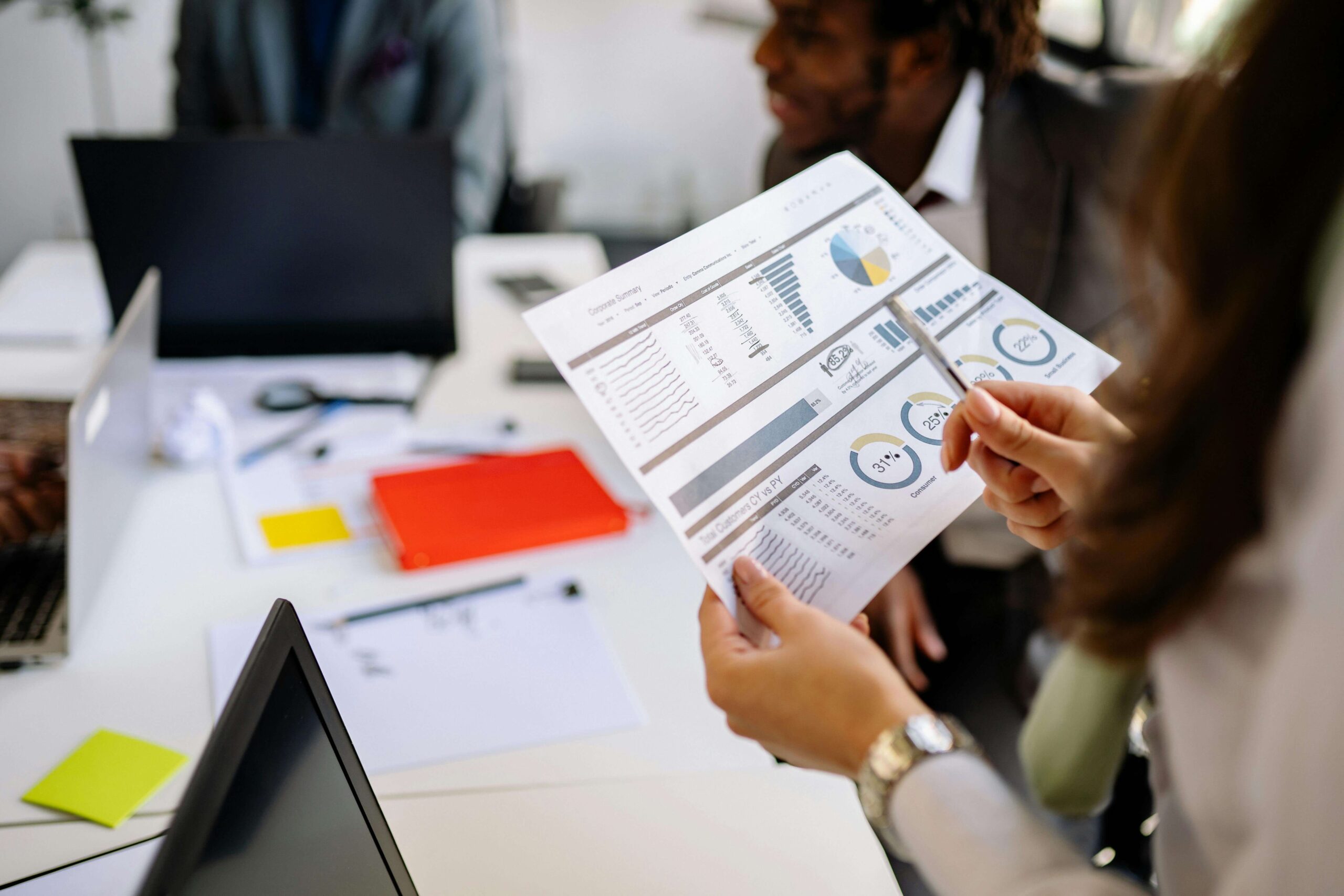
Conclusion
SBD’s partnership with Jodoo enabled a comprehensive transformation of their equipment management processes through advanced IoT connectivity and data-driven decision-making. By integrating multi-system frameworks with smart hardware solutions, they achieved real-time visibility into operations while significantly improving efficiency across maintenance workflows, vendor collaboration, and performance management.
As SBD continues its journey toward a fully realized Digital Smart Factory, the company sets a benchmark for leveraging no-code platforms like Jodoo to drive innovation and operational excellence in the manufacturing industry.
Ready to transform your operations like SBD? Request a Demo Today and take the first step toward building your own Digital Smart Factory!