98%
Custom Apps Built
$200k
Annual Cost Savings
2.5 Hours
Saved Daily Per Employee
Founded in 1847, Germany’s Siemens is a global leader in electrical and electronic engineering, consistently driving innovation across industries like manufacturing, infrastructure, transportation, and healthcare. With a revenue of $77.86 billion in 2023, Siemens ranked among the Fortune Global 500, reflecting its enduring influence and excellence.
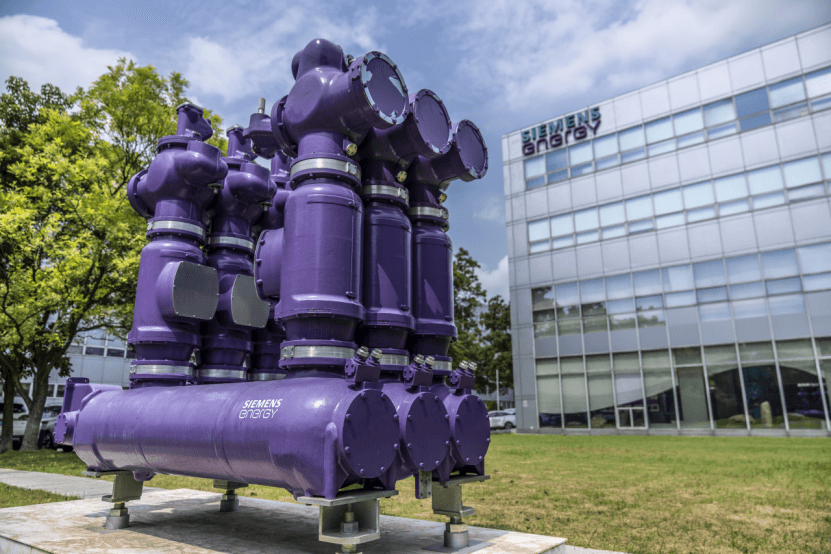
The challenges
Before adopting Jodoo, Siemens had implemented core business systems like SAP, MES, LES, and HR. Despite these systems, many operational scenarios—ranging from production processes to employee and asset management—remained unaddressed. Customizing core systems to meet these needs would have been both costly and time-intensive.
The solution
Based on the low technical barriers to no-code development and the quick hand-to-hand characteristics, after trial, the IT department decided to organize business units to learn to use Jodoo and give them permission to build applications. For more than a year, Siemens has independently developed 45 applications, covering production management, quality management, asset management, staff management, and eight other modules.
Building a strong foundation with an employee management system
The first application built with Jodoo was an employee management system tailored to meet Siemens’s unique needs. High-voltage switch products require customization and precise assembly by workshop employees, making labor costs a critical component of production expenses. The existing personnel management system fell short of these requirements, prompting the production department to independently design a new solution using Jodoo.
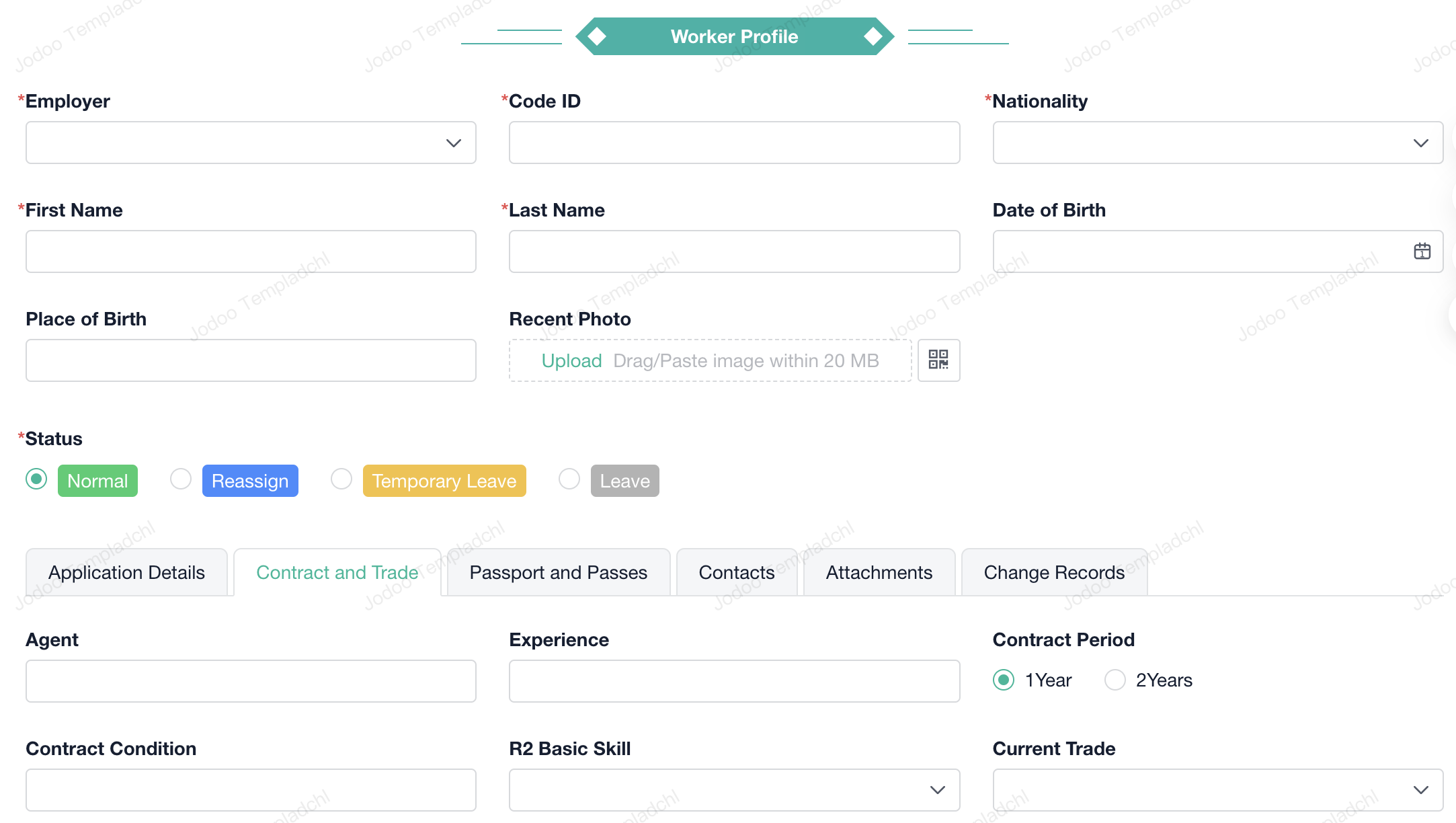
Safety lighting system improves the quality management module
Using Jodoo, the Siemens production department developed a safety lighting system, an FPY exception handling system, and an A3 reporting system to enhance its quality management processes. Each workstation in the factory features a terminal where workers can swipe cards to activate safety lights. This notifies foremen and technicians via mobile alerts to address issues in real-time. Once resolved, tasks can either be closed or escalated to engineers for further action.
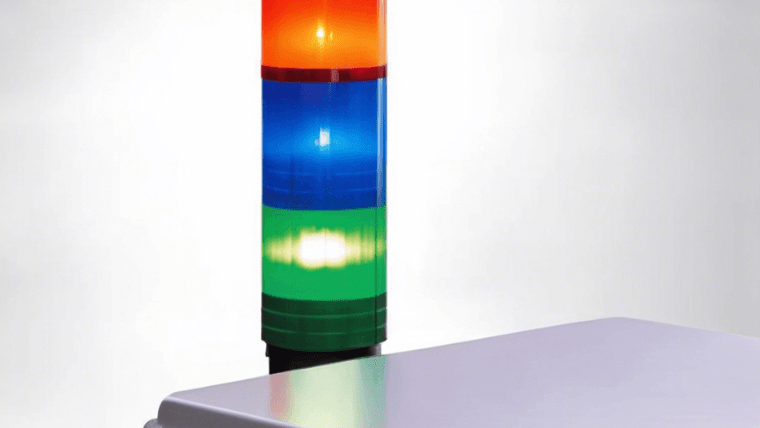
Optimizing 6S and 3I systems to create a closed-loop improvement process
Lean management is an important part of Siemens and is implemented through 6S and 3I systems. 6S audit is conducted every month, and the supervisor scores and records the problems through the Jodoo system. After finding the problems, the supervisor can directly initiate the rectification task to ensure closed-loop management.
3I management encourages employees to make reasonable suggestions and ensures that they are implemented. Based on the existing system, Siemens uses Jodoo to optimize the 3I process, where employee suggestions are first passed to the production supervisor, who determines whether support is needed and assigns tasks, resulting in a closed loop.
With Jodoo’s development, Siemens increased the efficiency of lean management, optimized the 6S and 3I systems, and ensured that the management process was responsive and closed.
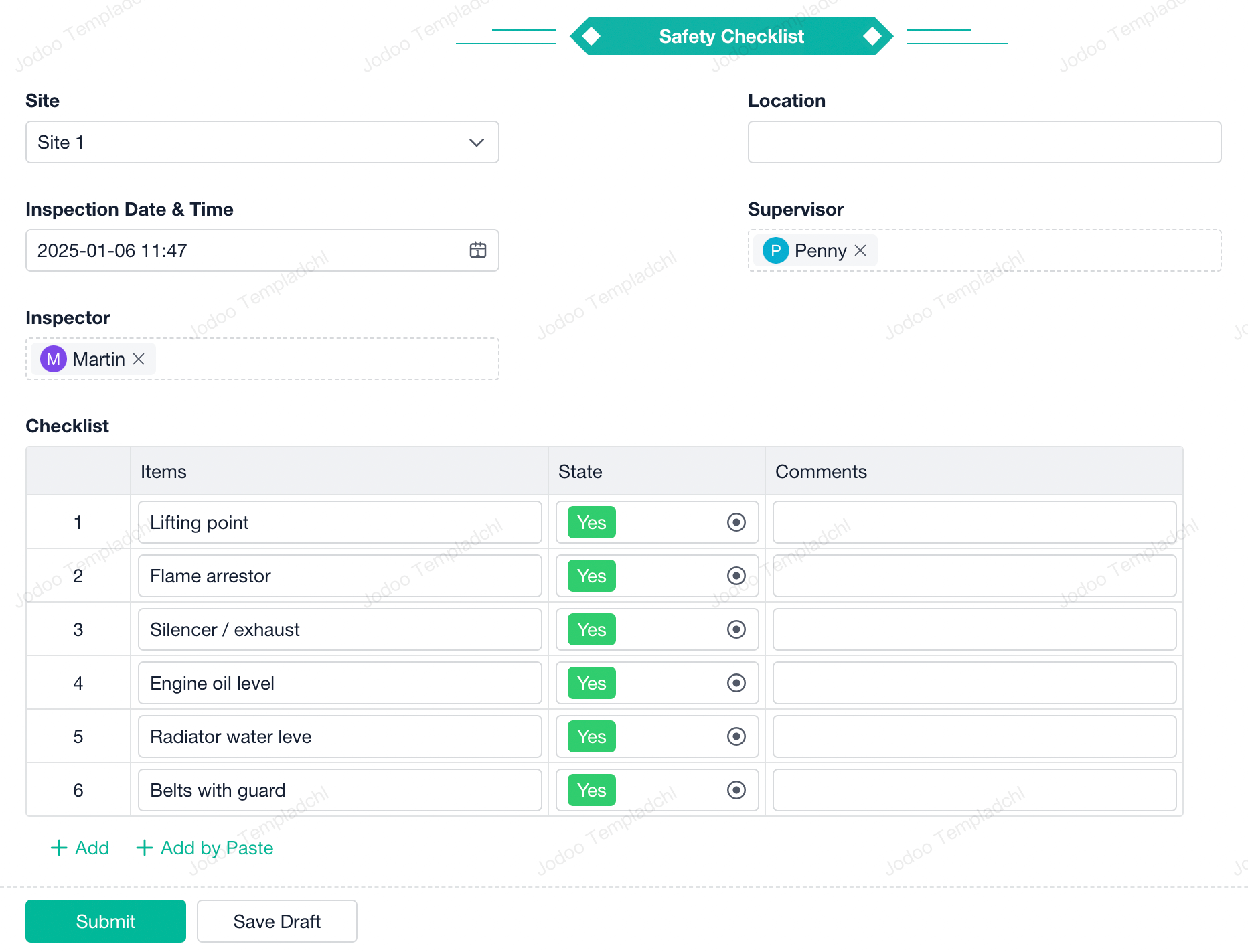
Project management system for ETO production
To manage its ETO (engineering-to-order) production model—characterized by small batches and diverse product variations—Siemens developed a project management system using Jodoo. Previously reliant on Excel spreadsheets and manual communication methods like phone calls and emails, project managers faced inefficiencies in information transfer. The new system assigns unique project numbers, tracks delivery timelines and customer requirements, and ensures seamless information flow across departments.
Through the project management Kanban, the project manager can view the project progress and delivery in real-time, prevent the risk of delay, and record key information such as drawings to form a traceable project management process.
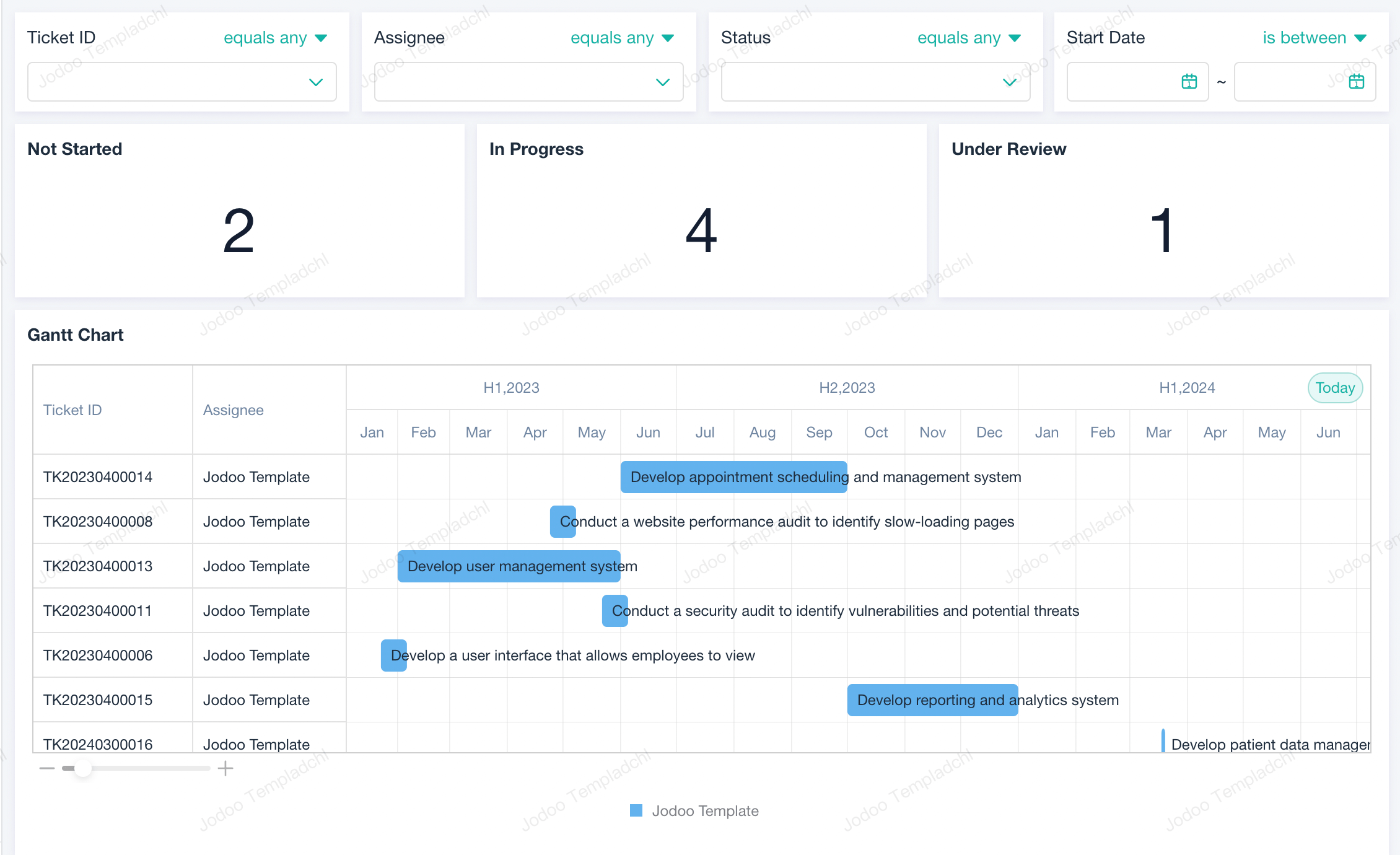
Jodoo is an efficient lean management tool that acts as a catalyst for innovation and a system cement in the company. Because no code development has low thresholds and fast iteration speed, department managers who are more familiar with the business can build a system that meets the actual needs. Through Jodoo, Siemens can quickly and efficiently digitize scenes that require inter-departmental communication, automatic reminders, and visual target management, and connect modules such as “man-machine material loop” in the factory to realize data interconnection.
Ready to accelerate your digital transformation like Siemens? Discover how Jodoo can empower your business with no-code innovation. Request a Demo Today.